This factory photo shows part of the New Assembly Hall in 1961.
Wheels – they are the early patterns for Triumph Heralds – from Sankey’s of Wellington* have been delivered and are being mated to tyres. On the left rear you can see rows and rows of wheels, a small batch of tyres on the right on the floor and finished wheels and tyres heading off on a conveyor.
***
*Joseph Sankey & Sons Ltd supplied a number of component parts for the Standard and Triumph range of cars, for the new Triumph Herald, launched in 1959, this included the chassis and road wheels. The firm was active from 1854-1983.
The origins of the business of Joseph Sankey & Sons Ltd are in the partnership agreed between Samuel Jackson and Joseph Sankey in 1854 for the production of blank trays from tinplate. Joseph Sankey was born in Bilston in 1827. After he was orphaned by the death of his father in 1836 he attended the Royal Orphanage School at Wolverhampton, and was apprenticed to John Duncalfe, tray blank maker of Hall Street, Bilston, when he was fourteen, where he was taught design and mechanical drawing. He was later employed by the Birch brothers who made tinplate trays that were then ‘japanned’.
After the failure of this business, two of the senior workmen, Charles Harthill, and Samuel Jackson, set up their own firm in Middlefield Lane, and employed Joseph Sankey. Charles Harthill died in 1854, when the firm owed £800 to Jon Bates, a sheet iron merchant. Bates secured possession of the plant and tools of the firm as security for the debt. He recognised Sankey’s skills and determination and persuaded Jackson to take him into partnership in 1854. This partnership took the decision to concentrate on the production of blank trays stamped from tinplate and then sold to japanners. Jackson & Sankey produced trays of different shapes and sizes, and had several ‘best-selling lines’. The business had to repeatedly remortgage the firm’s premises in Dudley Street to finance expansion, though was able to repay the loans.
In 1867, Joseph Sankey acquired land in Albert Street, Bilston, next to the back of the Dudley Street workshop. He had paid Samuel Jackson for his share of the partnership in 1861, but Jackson continued to work for the firm as a foreman in the blank tray shop. Large workshops were built at the Albert Street Works and steam-powered drop stamps were installed, enabling the firm to produce heavier gauges of metal to make frying pans and kettles. Workers were recruited from Birmingham and Wolverhampton to manufacture these products.
Joseph Sankey went into partnership with Richard Chambers and John Page to buy a rolling mill and ironworks at Stonefield in 1862 or 1863 in order to gain closer control over supplies of tinplate and sheet iron. The business was renamed the Bilston Iron Company. From 1874 the business concentrated on the manufacture and sale of a range of hollow-ware items including dish covers, tin boxes, lamps, lanterns, milk churns and chocolate moulds, and a huge variety of stamped or pressed metal products including bath tubs, metal life buoys, and fire shovels. The firm also developed a significant export business – exporting ‘Cassada’ pans to Brazil and bowls to india, Ceylon and China. Cassada pans were shallow dishes in which coffee beans were dried.
Until the late 1860s, Joseph Sankey did most of the book-keeping and paid the wages himself. In 1874 the firm had 65 employees. In 1871, Sankey’s eldest son, John William Sankey (1855-1913), left school to work in the offices, and he took on the firm’s accounting. He became a partner in 1878 and took on more managerial responsibilities to expand the firm. Sankey’s second son, George H. Sankey (1865-1934), joined the business in 1884. Two other sons worked for the firm briefly, before pursuing other careers. Joseph Sankey appears to have lived on the premises of the firm until the early 1860s, when he had a new home built, Goldthorn House, on Goldthorn Hill, Wolverhampton, where his sons were brought up. Joseph Sankey died in 1886.
The firm was contacted by a London iron merchant, Robert Jenkins, in December 1886, who had done some research into the possibility of making dynamo armatures from charcoal sheet iron discs and consulted Siemens the electrical engineers. Jenkins thought that the firm’s existing machines could be adapted to manufacture electrical laminations and persuaded Siemens to place an order for electrical stampings in 1887 through the firm Harold & Jenkins. By 1890, contracts had been concluded with several others firms, through the agents Harold & Jenkins, who were appointed Sankeys selling agents on a commission basis.
In 1893 the partnership of Harold & Jenkins dissolved, with Robert Jenkins continuing to work as an agent for Sankeys. The firm made improvements to their stampings during the mid-1890s, and abandoned charcoal iron in favour of a metal steel sheet which was given the brand name ‘Lohy’. This arrangement lasted until 1941, when the company decided that agencies were inappropriate, and a new company, Robert Jenkins & Sankey Ltd, was formed. John William Sankey admitted his two younger brother, Frederick Ernest Sankey and George Herbert Sankey, to the partnership in July 1891, as a result of the continuing expansion of the business. The name of the firm was changed to Joseph Sankey & Sons. The business continued to manufacture electrical laminations and also developed its traditional pressing and stamping business. Joseph Sankey & Sons acquired a number of smaller businesses during the 1890s including Edward Morris & Sons which manufactured sugar-making utensils; Huttons, which manufactured nickel plated trays; the Sanitary Bath Company, which made copper-clad steel; and the established firm of J. H. Hopkins & Sons of Granville Street, Birmingham, which was a hollow-ware and japanning company that had the ‘Sphinx’ trademark, subsequently adopted by Sankeys. The japanning side of this business was sold, and the stamping and pressing concentrated at the Albert Street Works in Bilston.
In 1890, Sankeys patented a process under the name of Neptune Ware’. This involved running tinplate through colour rollers to undercoat both sides. After being embossed and painted, the ware was blanked out to the final shape. The technique had been borrowed partly from America by John Sankey. This ware was used for waiters’ trays, ash-trays, cups, children’s money boxes, cake baskets and other small articles. ‘Neptune Ware’ was a huge success and part of the Albert Street Works had to be expanded to cope with the growing demand. During the 1890s, Sankeys were also producing more kettles than any other British company and made their manufacture cheaper by using steel, which could be pressed into shape more easily, speeding up production. In 1900 the ongoing expansion of the business led to the purchase of a derelict iron and tinplate works at Bradley, originally established in 1833 by Thompson, Hatton & Co. After the business failed, the site was sold to Sankeys. Most of the existing buildings were demolished, and new shops were built for slotting machines and keyway cutters in order to transfer the manufacture of electrial laminations to these renamed Bankfield Works from Albert Street. To meet the growing needs of the Bankfield Works, the Manor Rolling Mills at Ettingshall were purchased from Stephen Thompson Ltd in 1904. These premises were known as the Manor Works. The two plants were connected by the Shropshire Union Canal. Some of the mills had been converted by Thompson for the supply of electrical sheets, so Joseph Sankey & Sons was able to exploit this machinery and ensure a supply of sheets for the firm’s other works.
In September 1902, Joseph Sankey & Sons was floated with an authorised capital of £200,000 divided into 10,000 ordinary shares of £10 each and 10,000 5.5% preference shares of £10 each. George and Frederick Sankey were apointed directors, together with John Chambers, who had risen through the business to become, in effect, the company secretary. John Sankey became chairman. This post passed to his brother George after his death in 1913. Other members of the family were subsequently appointed to the board during the First World War years. In 1906, Sankeys and the Hadfield Steel Foundry Company of Sheffield entered into an arrangement whereby Sankeys were granted an exclusive licence to obtain or manufacture special electrical steel referred to as ‘stalloy’ as a registered brand. In 1909, Sankeys sub-licensed John Lysaght to roll sheets under Hadfield patents at their Orb Works. The firm also granted the Brymbo Steel Company, near Wrexham, a licence to make steel bars and blooms under the Hadfield patent on condition that these would then be sold to Lysaghts for rolling into sheet. Through these arrangements, Sankeys were able to increase their control over the supply and quality of their raw material outputs. Sankeys began to supply pressed body panels for automobiles in 1904, as well as wood and iron coachwork, necessitating the construction of wood-working body shops at Albert Street. The firm was also exporting body panels to Paris and New York by 1906. In 1908 Sankeys developed and patented the first pressed and welded, detachable motor car wheel, the ‘All Steel Wheel’. The firm also took orders for other automotive components, and demand increased rapidly, putting pressure on the Albert Street Works.
In 1910, Sankeys purchased the former factory of the Castle Car Company, at Hadley Castle, near Wellington, Shropshire. This company had supplied tramcars, and some of the machinery was still intact, making it possible to manufacture body panels there. In 1911, the body shop was transferred from the Bankfield Works, and the wheel shop moved from the Albert Street Works. The Hadley Castle Works was extremely successful, with the best-selling products being the Sankey wheel which was sold extensively to British car makers, and pressed sheet steel car and charabanc bodies. Sankeys contemplated entering into an agreement with Thomas Tilling of Peckham and W. A. Stevens of Maidstone which would involve the manufacture of omnibuses and lorries through the sale of the Hadley Works to the merged business, which would be called Hadley Engineering Company Ltd. A prospectus was prepared, and shares offered to the public, but the minimum subscription was not met, so Sankeys withdrew from the project. See DB-25/1/4 for papers relating to this venture. The firm was consistently successful during the Edwardian period; despite short-lived strikes and depressions, turnover and profit was increased. Sankeys lost large numbers of workers to the armed forces at the outbreak of war in 1914, and several branches of the business were severely affected. However, the firm received substantial orders from the Ministry of Munitions during the First World War, and from November 1915, the Albert Street Works became a Controlled Establishment under the authority of the Ministry of Munitions. Albert Street and Hadley Castle produced field kitchens, mine hemispheres, aeroplane parts and bombs, rifle grenades, mortar bombs anti-submarine bodies and shell bodies. They also produced steel helmets. In order to cope with this increased demand, Sankeys took on large number of female workers during the war years. Sixty-nine employees were killed during the war, including Sydney Sankey (1889-1915), the eldest son of John William Sankey, who was killed at the Battle of Loos. He was an engineer, and had been one of the directors of the company.
Although the company was still profitable in 1918, George Sankey, temporary chairman, had no desire to continue running the company. Other family members had their entry to the business postponed by war service. The majority of the company’s shares were owned by the family, and few managers had been recruited to board level. The firm had also not made enough allowance during the First World War for liability under Excess Profits Duty. Edgar Jones suggests that George Sankey was worried about how successful such a family company would be in the difficult economic conditions likely to follow the war years. Under these circumstances, George Sankey considered selling the company to John Lysaght, with whom Sankeys had strong business and social ties. John Lysaght & Co being one of the firm’s suppliers John Lysaght was a galvanising and sheet steel business with its origins in Bristol, but had expanded to include steelworks at Normanby, Scunthorpe and extensive rolling mills at Newport, South Wales. It had been founded in 1857. It was taken over by Henry Seymour Berry, D. R. Llewellyn, and Viscountess Rhondda in 1919. The Lysaghts were friends of Sankey family because the Lysaghts had owned two rolling mills, Swan Garden and Osier Bed, in Wolverhampton. A suggestion was made to George H. Sankey that Berry would buy Sankey shares. On 3 December 1919, Berry became the new chairman of Sankeys and Llewellyn also joined the board. Joseph Sankey & Sons Ltd became the sole subsidiary of John Lysaght Ltd. Berry was keen to be associated with Guest, Keen and Nettlefold and planned a takeover of that company. It was agreed instead that the companies should amalgamate. Therefore Lysaght and Sankeys became subsidiaries of GKN, and the merger was effective from 1 January 1920. All companies continued to operate under existing names and no new organisational structure was introduced, though membership of respective boards was revised. Sankeys retained its legal identity; policy was monitored by an exchange of directors, and informal rules regarding capital investment. The Registered Office of the company remained at Albert Street Works.
During the 1920s, the firm’s traditional market for manufactured hollow-ware was in steep decline. The cheap consumer goods that the firm had specialised in during the late Victorian period were no longer so profitable. More goods were being made from plastic, and more products were now being imported. Trade had recovered slightly by 1924, but the Albert Street works ceased enamelling hollow-ware, selling all excess stampings from the firm to Macfarlane & Robinson, enamellers, of Bushbury, Wolverhampton. Some of the traditional lines did maintain their popularity. These included the ‘Cassada’ pans sold to Brazil, and new pressed products manufactured at Albert Street during the 1920s included casings for petrol pumps supplied to W & T. Avery for Shell. However, more lines ceased to be produced in the 1930s when Albert Street Works went through a period of short-time working, and there were redundancies, as the company researched options for alternative products. Sankeys were still actively involved in acquiring subsidiary businesses.
The firm signed an agreement in the late 1920s with the Asiatic Petroleum Company and the Florence Stove Company, a UK subsidiary of the Florence Stove Corporation America of Gardner, Massahusetts, to make paraffin-burning heaters for the Florence Stove Company to sell. In 1938, Sankeys acquired a one-third interest in the Florence Stove Company, and after further acquisitions, obtained the outstanding interest. The company’s name was changed to the Florence Stove & Hardware Company, and the production of paraffin heaters became a substantial proportion of the output of the Albert Street Works during the 1950s. In 1929, Sankeys purchased Bath Street Works, formerly occupied by Holcrofts Steel Foundry Company, and subsequently by the Staffordshire Stainless Iron Company. These buildings were next to the Albert Street Works, and gained additional space for the factory. The site was converted to facilitate the production of steel wheelbarrows.
The revival of the economy from the mid 1930s encouraged the firm to modernise the Albert Street and Bath Street Works, with the installation of new presses and a boiler house and plant to heat the Works. Extensions were also made to the warehouse. The toolmaking and repair facility was located at the Bath Street site. Due to the decline in demand for the traditional lines manufactured by the Albert Street Works, the firm’s profits during the 1920s and early 1930s were concentrated in the Bankfield Works, which produced electrical stampings, and its supplier, the Manor Rolling Mills. Improvements were made at both sites, and E. W. Richmond was appointed as general manager at Bankfield in 1922. He made arrangements with electrical engineering companies whereby they obtained their components from Sankeys rather than manufacturing them themselves, and these companies invested in new machinery for the firm. Sankeys also began making stampings for wirelesses, and was able to tender successfully for laminations required by the new national grid established by the government during the early 1930s. A transformer strip shop was set up at the Bankfield Works, in a building that was also used by the company’s training school. In 1937, the Bankfield general manager and his staff also moved to the site from Albert Street, and a new office building was constructed. The Manor Works rolling mills were mechanised during the 1930s, and the first electric annealing furnace was operating by 1938. Plans were made in 1943 for the construction of a new laboratory at the Manor Works to test the grades and guages of electrical sheets. A research team was appointed in 1945 and the laboratory was eventually constructed in 1951 on the New Birmingham Road. It was known as the GKN Laboratory The Hadley Castle Works faced difficulties during the 1920s in collecting debts from unpaid orders, and in trading with car manufacturers struggling to sell what were seen as luxury products. However, conditions improved during the 1930s, and Sankeys installed three rim-making machines at the Works in order for the company to maintain its leading position as supplier of components to the automotive industry. By 1936,when the general manager, S. L. Brunton, retired, the labour force had risen to nearly 1,500.
In August 1939, Lysaght’s Constructional Department was contracted to extend the wheel department. Steel furniture was also being manufactured at the Hadley Castle Works, after T. E. Sellers, a director of Harris & Sheldon, a Birmingham shopfitters, entered into arrangements with Sankeys and E. Wentworth-Smith, to undertake the production of steel furniture under the brand-name ‘Sankey-Sheldon’ in 1917. The first sales office opened in 1919. Sankeys acquired a share in Harris & Sheldon in 1926, and George H. Sankey was elected to the Sheldon board. Sankeys had also purchased the rival company of Crittals of Braintree in 1920.
In addition to automotive components and steel furniture the Hadley Castle Works also developed subsidiary product lines during the 1930s, including steel barrels for the palm oil trade in Africa steel roofing sheets supplied to the Rubberoid Company for decking, radiators, metal trim, bath panels and steel pulleys. Despite being a subsidiary of John Lysaght, itself a subsidiary of GKN, ‘Joseph Sankey & Sons retained a high degree of autonomy in the practical running of the business’. GKN and Lysaght directors sat on the Sankey board, but members of the Sankey family and senior managers appointed to the board made strategic plans which were also discussed with their colleagues.
George H. Sankey remained the effective head of the business until his death in 1934. His brother, Frederick Sankey had also become a director on the flotation of the firm in 1902. George H. Sankey’s three sons, Harold B. Sankey (1895-1954), George Ronald Sankey (1900-1987) and Geoffrey B. Sankey (1908-1983) had also joined the family business. Harold B. Sankey became assistant to S. L. Brunton at the Hadley Castle Works following service in the Field Artillery during the First World War and a degree in mechanical science at Cambridge. He became managing director on his father’s death and moved to the head office at Albert Street. Between 1942 and 1944 he was appointed by the Ministry of Production as Regional Controller for the Midlands, when his brother Ronald Sankey took the position of managing director. He continued to serve as managing director until his death in 1954; he had become chairman in 1951. Ronald Sankey worked at Manor Rolling Mills and was elected to the board in 1929. He became general manager at Manor Works in 1941. In 1943, he took on the management of Bankfield Works, and remained in that position unil his retirement. Geoffrey B. Sankey had trained as a barrister, and worked at the head office at Bilston. He was transferred to Hadley Castle in 1934, enabling his brother Harold B. Sankey to move to the Albert Street office to take up the post of managing director.
Sankeys built up a strong relationship with the communities of Bilston and Wellington, Shropshire from the early days of the business. The Sankey brothers organised annual outings for their employees, and there was a staff canteen at the Albert Street Works from 1892. A sick benefit club was also set up, to which the firm contributed £25 a year. There are suggestions in company histories that a sports club was first founded in 1893 (see DB-25/7/3/1), and that from 1913 employees from Albert Street, Bankfield and Manor Works were participating in company sporting activities. In 1935 land between Albert Street and Bankfield Works, purchased by the firm in 1921, was levelled to lay out a sports field and pavilion for the Sankey Social and Sports Club. In 1938, a contributory staff pension scheme was established with the Prudential Assurance Company. As well as football and other sports teams, the company had its own St. Johns Ambulance section, and fire brigade from 1958, and a Home Guard and Works Fire Fighting organisation during the Second World War and a Works Fire Fighting organisation. The Social and Sports Club also organised entertainments including dances with live bands, bingo, and other entertainments, and was very popular during and immediately after the Second World War period, possibly partly because entry to the club was not restricted to Works employees. Evidence from in-house publications consulted by William Moorwood in his history of the company and from copies of ‘Sphinx’ magazine in this collection shows that a number of societies and social groups were formed by workers at Sankeys, including choirs, ballroom dancing groups, music groups, and other clubs focused on hobbies and leisure interests.
Sankey’s manufacturing plant was in heavy use during the Second World War. Sankey had been dealing with government orders since the mid 1930s, but during the war years a number of extensions were made to the building and plant, largely funded by the government. New buildings were constructed at Albert Street to manufacture aeroplane spinners for De Havilland and Rotol, and parts used in jet engines for the De Havilland DH1. By the end of 1940, 85 per cent of the company’s output was directed to war work. The labour force was hugely increased, with many men being retained under ‘reserved occupation’ regulations, and large numbers of women workers recruited. New canteens and assembly rooms had to be constructed at Albert Street, Bankfield, and Manor Works. In addition to aeroplane parts, Sankeys were also producing heavy wheels for army vehicles, ammunition boxes, steel helmets, bombs, mines, depth charge cases, charges and throwers, spinners for aircraft, complete spitfires, bridge sections and floats for the Admiralty. The firm also manufactured electrical stampings for wireless sets and radar, and supplied steel furniture to the Royal Navy. In 1944, Sankeys was still engaged to maximum capacity on war work, but orders began to decline after the end of hostilities in Europe in May 1945. The company had expanded and diverted their factories for war manufacture and a period of adjustment to peacetime conditions followed.
Sankeys continued to move into new areas of manufacture during the post-war period, and much production was centred on the Hadley Castle Works. A new wheel shop was built there in 1946, with further extensions in 1955 and 1959. The company diversified into the manufacture of agricultural implements in 1947, including trailers, tractors, parts, ploughs, seed drills and other aids to mechanised farming. In 1958 a new steel furniture factory was built. The Commercial Cab Shop commenced production in 1961, and the GKN Board approved a £3.5million capital investment at Hadley Castle Works for the production of road wheels for cars, trucks, buses and tractors, as well as cabs for Leyland. Another new wheel shop warehouse and paint plant commenced production in 1967. The Hadley Castle Works also began producing mobility vehicles for people with disabilities, and armoured vehicles including the ‘Warrior’ tank manufactured through GKN Defence. The company also moved into the manufacture of vending machines during the 1960s. The Automatic Vending Division of the company made a range of hot and cold beverage and snack machines, including the Sankey Mark VII. The firm also sold a range of cups and ingredients including the Kingsway range developed for use in Sankey machines. The company had acquired Universal Brewery Equipment Ltd in 1954, and now increased production of beer packaging, particularly Combination Units for kegs to be washed, sterlised and refilled, as well as the kegs themselves. These products were known collectively as the Sankey System. The Plastics Division produced plastic mouldings for the automotive and construction industry, as well as for domestic appliances, televisions radios and office equipment. The company also continued to produce steel furniture for marine cabins and accommodation modules for oil rigs as well as producing partitioning for general office and factory use through the Sankey-Sheldon Division. Production continued at the Albert Street Works, although on a smaller scale than before the war.
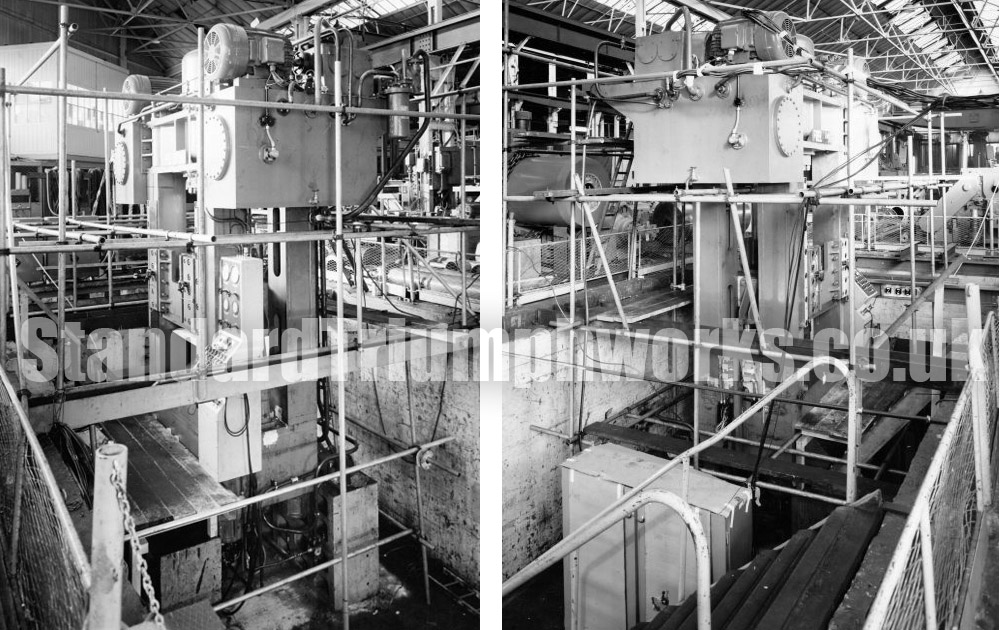
A complete re-build of the Works took place in 1957-1958, with the demolition of old buildings, and the construction of a new head office. The location of departments within the plant was also re-organised. The Manor Works were formed into a separate Limited Company in 1949 and extensions continued up to 1952. In 1968, Joseph Sankey & Sons Ltd became known as GKN Sankey Ltd. By 1970, Hadley Castle Works had taken over from Albert Street Works as centre of Sankey operations, with a workforce of 5,054 employees as opposed to 1,575 at Albert Street. Bankfield Works was also functioning during this period, as well as smaller factories managed by the firm. These included works at Porter Street, Dudley, set up in 1952 for the production of plated bumper bars and overriders and a production plant at Cardiff. There was also a site at Hereford, known as the Rotherwas Works, established in the 1940s for the manufacture of jet engine components and small motor stampings as well as Florence Stove parts and beer barrels. For a time, during the 1950s, there was also a Works at Cannock which was established to cope with extra demand for production space for oil stoves and radiators, but the factory closed in the early 1960s. There were also small factories at Brownhills, Kingsbury and Bordesley. Some of these factories came into the company’s possession through its acquisition of subsidiaries.
In 1971 Sankey took over manufacture of earthmover and heavy wheels from Dunlop. Dunlop took over Sankey Car Wheels. The company was split into divisions comprising: Wheel; Pressings; Bankfield; Plastics; Brewery; Unistrut; Sankey Sheldon; Automatic Vending; and Sub-Group. The Bankfield division continued to produce electrical laminations used in domestic and industrial motors. The Sub-Group headquarters was at Hadley Castle Works. Sankeys established a number of overseas subsidiary concerns during during the 1940s and 1950s. The first of these was a factory in India, after gaining approval from GKN, which supplied Crompton Parkinson with electrical sheets and stampings. The factory was set up at Worli, Mumbai (Bombay), and a new company, Sankey Electrical Stampings Ltd, was formed. Operations began at the Works in 1944, and a second factory was construted at Shalimar on the outskirts of Kolkata (Calcutta) in 1945. The Mumbai factory was transferred from Worli to GKN’s site at Bhandup in 1946.
In 1950, the company opened an electrical laminations factory in Newcastle, Australia, and a factory for the production of steel furniture in Johannesburg, South Africa. In 1952, a factory for both electrical laminations and steel furniture was established in Canada, at Smith Falls, Ontario. Sankeys developed a business relationship with other GKN companies both before and after the Second World War. The company acquired a set of buildings at Dudley transferred by another GKN company, IONIC, which specialised in chromium plating. Production continued here under the name Sankey Plated Pressings. Sankey-Oberg was formed in 1961 to design and manufacture special dies in tungsten carbide at premises situated just outside Dudley town centre. GKN purchased Projectile Engineering Company Ltd of Battersea, London and the production of metal pressings divison was moved to Sankeys Works beginning in 1964. Welding equipment, presses and units for pedal production were moved to Manor, Albert Street and Hadley Castle Works.
The collection includes significant amounts of financial and production records of Bayliss, Jones & Bayliss Ltd, a long established Wolverhampton metalware company which was taken over by GKN and operated as Sankeys and John Lysaght did, retaining its identity under the GKN group umbrella. Like Sankeys, the firm kept its name until 1968. The presence of Bayliss, Jones & Bayliss Ltd records in this collection, and references in William Moorwood’s history of Joseph Sankey & Sons Ltd suggests that the two companies were connected through their membership of the GKN group. For example, Moorwood states that a secretary at Bayliss Jones & Bayliss Ltd was seconded to Harold B. Sankey in his capacity as Midland Regional Controller for the Ministry of Production for the duration of the war, and that she also worked at the Albert Street Works before returning to work at Bayliss, Jones & Bayliss Ltd . The fabrication business previously carried out at Manor Works was transferred to a vacant building belonging to Bayliss, Jones & Bayliss Ltd at Cable Street, Wolverhampton when Manor Works was re-equipped for plastic moulding in the 1970s.
By the 1970s, the company was losing orders, and the Manor Works were closed in 1978, as were parts of the Bilston Works. There were also redundancies at Hadley Castle Works and Bilston in 1980 and 1981 due to massive losses in the Wheel and Pressing areas. In 1981 the Hadley Castle Works Toolroom was reduced to 200 employees. Albert Street Works closed in 1988, and the Sports and Social Club also closed. Buildings at the site were demolished. The brewery business was sold and Presses were moved to the Hadley Castle Works to be installed in a vacant building as part of a joint venture with Jaguar Company to be known as ‘Venture Pressings’ to produce Body Presings. Hadley Castle Works was formed into four operating units comprising; Light Fabrications, supplying telephone kiosks; Agricultural Products, supplying tractor cabs for Ford and Massey Ferguson; Engineering Products, producting car components; and Wheel Division concentrating on tractor and off Highway wheels. More design work was undertaken for military vehicles, but the venture with Jaguar failed when that firm was taken over. The Defence and Military business was sold to Alvis, and the name of the business at Hadley Castle was changed from GKN Engineering Products to GKN Auto Structures in 2001. Ford and Massey Ferguson ceased production of tractors, so the main agricultural business came to an end in 2002 and the GKN Cabs Division closed. In 2004, a local celebration was held at the Hadley Works to mark the 150th anniversary of the founding company, Joseph Sankey. There were still 1,600 people employed at the plant. There is evidence that laminations were still being produced in Bilston until 2005 when Corus closed the Sankey Laminations factory there with the loss of 190 jobs.
National Archives